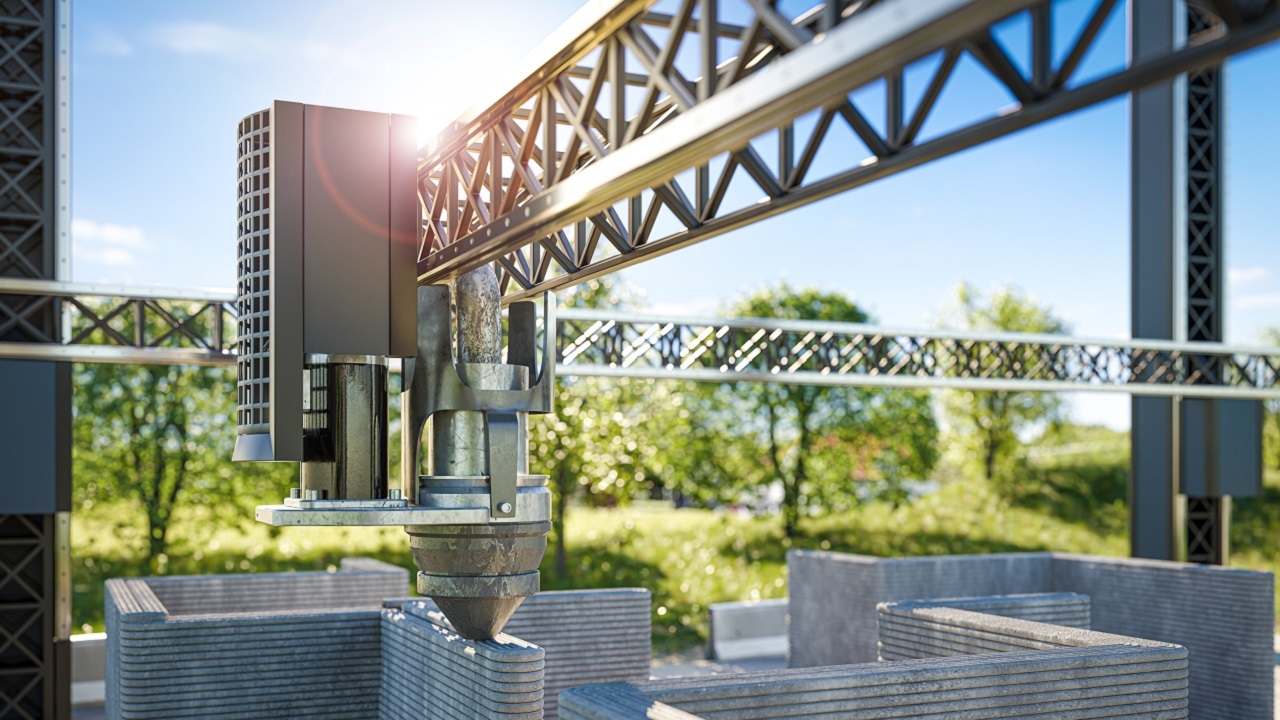
3D concrete printing (3DCP) may be one of the most disruptive technologies in the construction industry since the advent of steel-framed skyscrapers.
3DCP is still in its infancy in the US, with the first occupied 3D printed house unveiled in December 2021, but California will soon have the country's first neighborhood of 3D printed houses.1 Around the world, 3DCP has been used to construct shops, schools, office buildings and even bridges. In 2022, the global market was only $169M,2 but it's expected to have a compounded annual growth rate of 101.9% from 2023 to 2030.3
How 3DCP works
3D concrete printers are robots that extrude layers of mortar-like material, with each layer bonding to the prior layer to create walls and other desired shapes based on a computer-aided design (CAD) or building information modeling (BIM) model. No forms are necessary because the material holds its shape as it's laid down. Until recently, ordinary concrete didn't work with many printers, but recent developments allow use of standard concrete with additives that make it suitable for printing.4
Printers come in two basic types — Gantry and Robotic arm. Gantry-style printers sit over the print area and move a printer head or nozzle along x, y and z axes. Robotic arm printers move the nozzle on a crane like structure that can move along more axes.5 Gantry printers can print larger areas while robotic arm printers are more compact and easier to set up, and can print with more detail.
Printers can create foundation layouts for excavation and then print the foundations after underground mechanical, electrical and plumbing (MEP) are installed. A conventional slab can be poured, or the slab can be printed around the stub-ups as in traditional construction.6 Next, basement and other walls are printed.
Openings for doors and windows can be cut out before the material has fully cured. Smaller items like plumbing sleeves and electrical boxes can be inserted during the printing process, so that material flows around the sleeves and boxes without any gaps. The material is troweled smooth before it sets — usually within three hours of printing.7
Each wall is printed as a double wall with space in between. Panels are created within the walls to provide access for MEP rough in. Finally, spray foam insulation can be sprayed into the wall cavity to provide insulation.6
Benefits of 3DCP
3DCP has significant advantages over traditional construction, some of which — such as cost and safety — have implications for insurers.
- Cost. Printing requires two or three workers to operate the machine, rather than all the workers involved in assembly, stripping formwork and framing walls.8 Material saving are also significant: one company used just $6,000 of materials to print a 1,900-square-foot home in January 2020.9
- Speed. Each of the 1,450 square-foot-houses in the California neighborhood mentioned in the introduction took about 24 hours to print before the MEP and finish trades start working.
- Environmental impact. Most construction creates waste as standard items like lumber and drywall are cut to the desired size or shape.10 Because in 3DCP the only necessary material is used to create the shape, there's much less waste.11 3DCP can also use locally sourced material to avoid greenhouse emissions from transportation. In Dubai, a Danish manufacturer built an 871-square-foot coffee shop with 22 hours of printing time, using concrete made of 99% locally available raw materials.12
- Design freedom. 3DCP structures can be constructed to resemble any structurally sound shape.12 Recent developments include use of multiple nozzles to provide "quick and precise color changes."13
- Safety. Because the machine does the work, workers are exposed to fewer hazards.14
3DCP challenges
Despite all 3DCP's advantages, it does face several challenges:
High initial investment costs and long lead times. 3D printers are expensive (from $250,000 to $1 million) and generally not yet available off-the-shelf, with advertised wait times of six months.
Building code hurdles. Many of the prescriptive requirements in common building codes don't apply to printed construction.15 No ASTM International or American Society of Civil Engineers (ASCE) standards apply, so materials can require multiple rounds of testing to obtain building official approval.16
The International Code Council recently adopted Appendix AW, stating that 3D-printed buildings "shall be designed by an organization certified in accordance with UL 3401 by and approved agency and approved by the building official."17 Under UL 3041, a certified professional produces a report that evaluates the proposed project and creates a custom specification. The building official then considers the project under the alternate materials and methods provisions of the building code. While this hurdle is cumbersome now, 3DCP should become standardized over time.
Limited print size. Printed structural sizes are currently limited by the size of the machines. Work continues on developing vertical printing — the first two-story 3D printed building was finished in September 2022.18
Lack of tensile strength. Most concrete structures are reinforced with bars or post-tension cables. In 2017, the Dutch created the first reinforced, pre-stressed printed concrete bridge.19 Our research found no cases of post-tensioned printed concrete and only limited experimentation with rebar.
3DCP risks
3DCP presents new risks that the construction industry will have to address. In addition, because underwriters have little to no experience with the technology, they'll need to be educated so they can assess the risks across various policies.
- Approval delays. Obtaining building official approval under Appendix AW is a lengthy and uncertain process.
- Mechanical breakdown. Delays can cause problems with bonding if a layer hardens before the next layer can be laid.14
- Cyber. File corruption, hacking and other data issues can stop the print or cause printing defects.14 Data must be protected and cyber coverage tailored to 3DCP cyber risks.
- Design modelling. Print sequences will need to be organized so that printed material doesn't get in the way of further printing.20
- Seismic issues. Systems need to be developed to provide reinforcement in seismic areas.21
- Labor issues. Unionized contractors will need to consider jurisdictional disputes, and prevailing wage projects will require wage determinations for printer operators.
- Contract issues. New contract forms need to be developed and updated to reflect anticipated risks and those that emerge with experience.22