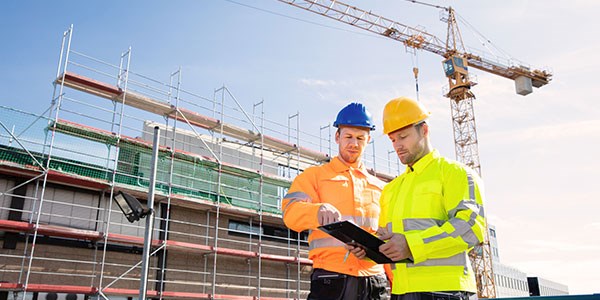
During Covid, very little was moving, but as businesses started to open up again, the challenges of importing materials after Brexit started to become apparent. The cost of import grew substantially, but also supplies were limited and delivery was taking much longer.
These challenges were in many ways a double edged sword, the upside was that local suppliers were now finding greater demand for their goods, and less competition from overseas suppliers. However, demand soon began to outweigh supply, which in turn forced prices even higher, and contractors were finding it more and more difficult to obtain materials on time, which in turn led to delays in completion of projects.
A further complication was that during the lockdown period and shortly after, many contractors were offering fixed price tenders to maintain turnover and keep their workforce employed, but as the cost of materials began its upward spiral, many of these contracts, which had been agreed with very low margins, began to tip into loss making projects. With no room for manoeuvre, and little sympathy from employers, this sent many contractors perilously close to the brink.
The sudden downturn in the economy then created a perfect storm, and we have now seen greater numbers of contractors, some of which were very long established and well regarded businesses, with seemingly healthy order books, fall into administration.
For the ones who remain, whilst some of the issues with materials costs have now stabilised, finding a secure and reliable supply chain remains a huge challenge.
One of the success stories to come out of this adversity is that recycling and repurposing used building materials is now becoming more common place. This has the added advantage that a sector which is one of the biggest creators of carbon emissions is now becoming greener. Though to some cynics this is borne more out of necessity than any altruism on the part of the construction sector, the net result is the same and certainly assists the UK’s aim to reach net zero.
This has accelerated research into alternative resources, and the use of different materials, and while some of these are of concern to insurers, and tend to be more expensive than materials that are more traditional at present, they are beginning to become more mainstream. As insurers start to establish an understanding of these, and build up a history of how they perform in the event of an insured peril, particularly fire or water damage, these types of buildings will become easier to insure and covers will become more readily available.
It could therefore be argued that the severe shortages of supplies experienced over the last few years has significantly helped to reshape the construction sector and focus on more sustainable and local supplies of materials, in a way which is now becoming a permanent change.
How Gallagher Can Help
From simple phone-based advice to bespoke consultancy, packaged services and training, we can provide advice and services that could make a real difference to your organisation. We do this in a way that links your legal obligations to your insurers’ expectations – affordably, accurately, and sustainably.